The solution of general field problems
With regard to nuclear verification, the finite element method is mainly used in strength calculations as well as for the simulation of flow processes and general thermal processes. More than two decades of calculation experience in this field have resulted in extensive know-how for solving a wide variety of problems. Depending on the problem, we develop individual concepts and verifications in compliance with the applicable regulations.
KAE GmbH uses the commercial FE program system Ansys to carry out structural-mechanical analyses. The components or structures to be analyzed are always mapped in three dimensions, as this is the only way to accurately evaluate the real situation. In addition to simple, static, linear-elastic strength analyses, dynamic analyses with elastic-plastic material behavior under the influence of temperature are primarily carried out today - thanks to powerful PC systems.
Application example Strength
The following example shows the force transmission of a pipe clamp to a pipe or the pipe cam. In addition to the external mechanical load on the pipe clamp, the simulation result here is determined in particular by the mapping quality of the clamp/pipe contact problem.
Modal calculations
To determine and evaluate the dynamic behavior of components and structures, an eigenvalue analysis, i.e. the calculation of eigenmodes (natural frequencies and shapes), is first carried out. Together with the specific damping parameters, quantitative statements can be made about the vibration behavior of the components under dynamic load, e.g. earthquakes.
Fatigue analyses
The fatigue of materials and components is an important, safety-relevant issue in the case of cyclical mechanical and thermal loads and is therefore an essential part of serious ageing management. Fatigue analysis is the only way to demonstrate and prove fatigue strength and operational stability and thus rule out component failure due to fatigue.
In the following example, the calculation results (degree of fatigue) of the detailed method of "general elastic-plastic fatigue analysis" from KTA 3201.2 are compared and evaluated with the results of other, less detailed methods of fatigue analysis according to KTA 3201.2 or FAMOS level 3.
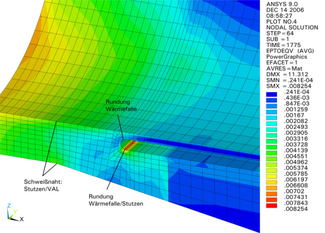
Fracture mechanics analyses
Fracture mechanics analyses can be carried out in two different ways. The first method is based on the analysis of the stress state in the undisturbed component, i.e. without a crack, using classical FE analysis, as described under "Strength calculation". Using subsequent, usually empirical analysis methods, a critical crack size can be determined as a function of the prevailing stress state.
A much more precise method of evaluating existing or postulated cracks is to determine the fracture mechanical parameters such as stress intensity factors and T-stresses. These values can also be used to make a reliable statement about the crack propagation or the remaining service life of a component under certain loads.
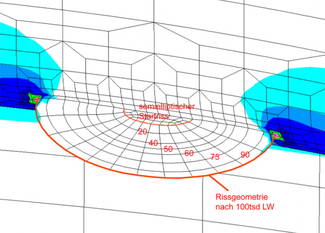